Plant 5, the largest single investment to date, was designed not only to increase production capacity by 30 percent with an additional 2,500 square metres of production space and thereby meet the continuing high demand for Franke CT bearings. The new building was also a further step towards restructuring the company according to product groups and introducing a matrix organisation.
The 72 metre long and 24 metre wide BUILDING is quite literally underpinned by 450 piled foundations, which were driven up to ten metres deep into the ground in 2016. Sections of the 40-centimetre-thick concrete floor slab were separated from each other to prevent subsequent vibrations. The shopfloor and reconditioning areas form the core part of the plant. This is where the production teams of the highly dynamic special bearings division, which is now concentrated here – employees from ring production, machining, bearing assembly, quality assurance and dispatch logistics – can meet and coordinate without losing time to travel. The hall was completed in July 2017 and put straight to use for a staff meeting and a summer party. The machines were installed by the end of the year, some of them being new, others being brought in from other plants.
Among other things, this freed up space in Plan 4 to take the matrix organisation that has already been introduced in the assembly of special bearings a further step towards the future by bringing them together (after a major renovation in 2022): All employees in this product group, from Design to Procurement, Work Preparation, Quality Management and Production, moved closer together on one floor – including a shared break area. This already corresponds to the “Matrix 3” organisational form, i.e. the bringing together of mental and manual work.
Firstly, the matrix organisation optimises the value streams in the company by virtue of its flat hierarchies and efficient links. Secondly, through its flexibility and adaptability, it also heightens customer focus and delivery reliability, improves coordination and communication, increases employees’ expertise through close collaboration and utilises resources more efficiently. For example, across the entire production process, paper has largely been replaced by screens at the workstations.
Franke is currently working hard to expand the matrix organisation into other areas of the company. The current organisational chart is a visual representation of the extensive transformation, in which flat hierarchies, the matrix and new specialist areas such as lean management and digitalisation can be found. //
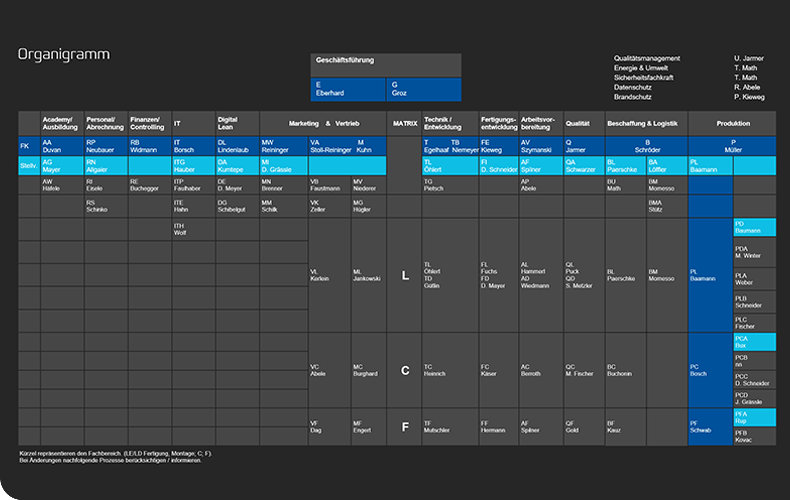
The matrix organisation completely redefines how we work together; it serves to increase agility, quality and customer focus and ultimately also ensures greater employee satisfaction
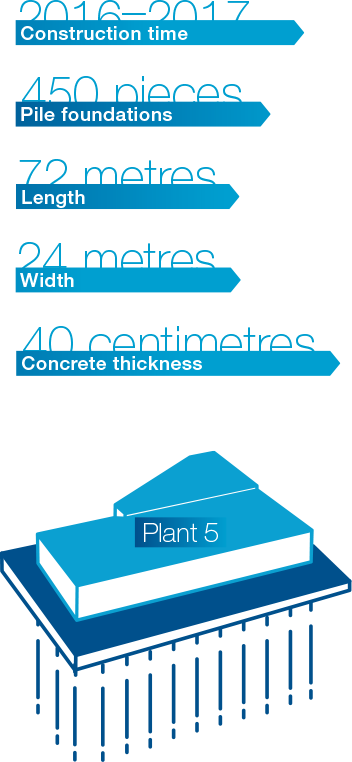